Recently, the BBC has announced a new initiative at the London Zoo,
which makes animal x-rays available to attendees, extending beyond the
presentation of the work of veterinary surgeons, and primarily intended
for general educational purposes.
Here, in Pecs, officials have stretched their imagination far beyond
the London Zoo, resulting in the dimensional printing of animal bones in
association with the staff of the 3D Print Technology Center of the
University of Pécs (PTE).
"We were awarded the contract, of which was orginally solicited to
participating entities throughout the region and hosted on behalf of the
CIty Zoo, Pécs, and the preparation was an exciting task from a
professional point of view, since we were in a ”terra incognita” in many
areas," admits Laszlo Szaloki, Project Manager of the PTE 3D Center.
“We needed real teamwork within PTE, and we took advantage in seeking
the support from many individuals, and avoided limiting ourselves to
those currently employed in the 3D center. For example, do you know what
a 3D teething of a hippopotamus really looks like? Today we know. The
expenses had to be accurately estimated, which was also not an easy
task, and it required intensive follow-up to determine what kind of task
we actually had accomplished. We had to know how large the workpieces
will be, i.e., how much material and time will be needed, not to mention
digitization, planning, printing supervision, and post-production work.
”
No Animals Were Harmed During this Project
The actual work regarding the various pieces was originally
initiated by Viktor Potari, and later followed by Bence Mánfai and Tamás
Bulsz, who eventually took over the task. "Not one single animal was
harmed during the project," explains Tamás Bulsz. ”W we worked with
bones, and animal remains, not living animals. The collection of the
samples was an interesting topic in itself, since they originated from
manydifferent places. The Natural History Museum, the Tropicarium, and
several zoos all generously sent original bones or remains.”
As of yet and to the knowledge of the staff in association with the
3D Print Technology Center, there has not been a similar project in
Hungary. “I had to solve challenging problems in every respect, however,
I can't report any difficulties since the individual steps of the
technology are fairly well known. From the 3D scanning (imaging) through
the creation of printable 3D models, the steps of the process are
customary, up until printing, and we only have to properly apply them
for this non-standard task. Most of the time was spent towards creating
the actual 3D models. Following digitization, the scanned files had to
be "cleaned up" and segmented, taking into account the anatomical
features. In particular, the dimensions (very small or very large) and
unusual anatomical structures – since we are far more familiar with
human anatomy - caused some headaches,” summarizes Bence Mánfai.
The largest workpiece was the hippo skull, which is more than sixty
centimeters long and forty centimeters wide. The 3D model had to be
”sliced” into segments according to the capabilities of the printers,
bearing in mind they will be glued together later in the future. In
regards to the smaller ones, the main problem was the likelihood smaller
parts will be too fragile, as they were designed for illustrative
purposes, i.e., they later will be handled by children.
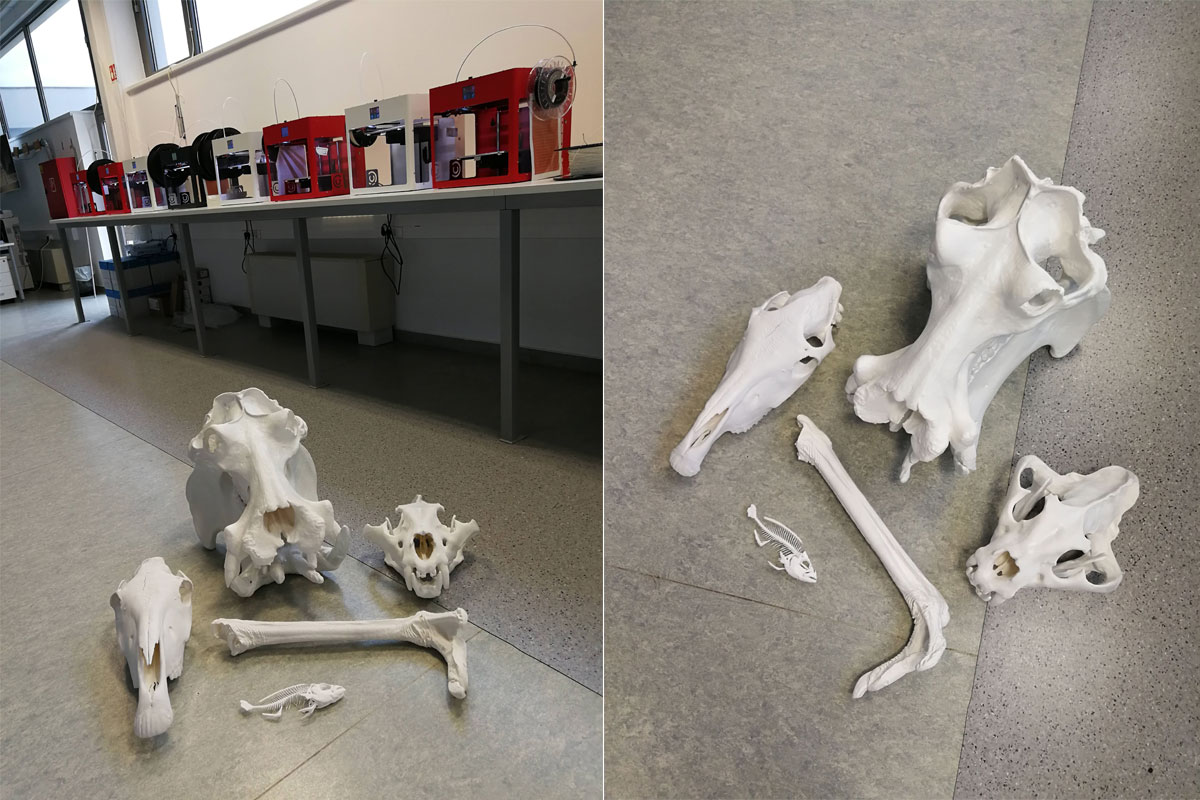
Hippopotamus in Flake Weight
An important feature of the printed "bones" is emphasized in their
physical weight, since they are considerably lighter than the original,
thus, in reference to the hippo's skull, the weight of the printed
version is only one-third of the original. A single person can move,
rotate, and comfortably lift the skull, unlike the original. They have
also made experiments using the material of the subject, trying to
determine the best compromise between durability and weight. Precision
was also a very important factor in the modeling phase. Although the
staff of the center are accustomed to this, special demands have also
emerged, such as the particularly vivid reproduction of teeth, as
students are presented with the features of different teeth regarding
these models. The creators of 3D models have committted immense time and
effort towards enhancing characteristics, such as teeth, lending
authenticity to the end product.
The staff of the center used two printing technologies. FDM
(filament) was chosen for the larger models, and SLS (Selective Laser
Sintering) printing for the smaller, yet more detailed workpieces. The
resolution was two and three tenths millimeters per layer, dependent
upon the level of detail required. During the post-production process,
the main task was to remove the visible joints, smooth out the rougher
surfaces, and eventually paint the models characteristically using hues
ensuring a high level of realism and naturalness.
In spite of astonishing lifelike replicas, archaeologists of the
future will likely easily avert confusing the printed hippopotamus bones
with the later physical remains of the two hyppos, Ágnes and Ágnes, who
currently reside at the City Zoo in Pécs.
"There is still little experience concerning durability, however, the
applied polyethylic acid (PLA) base material will eventually break down
after a while, so we are not expected to cause a breakthrough for
tomorrow’s archaeologists," states Tamás Bulsz, laughing. “However, I
predict a span of 20-25 years of lifetime. Twenty years later, it will
be worthwhile to continue this conversation, and I can tell you exactly
how the skulls absorb the stress and the passing of time. ”
It will probably be possible to refine the technology, as the City
Zoo expressively are satisfied with the "bones”, thus far, and the
possibility of future cooperation has already been discussed.
Gabor Szabo