The primary mission regarding the 3D Printing and Technology Center
is now aligned with the Senior Leadership’s recent decision to chisel a
new “umbrella organization” in support of research and development.
Strategically, the newly organized entity will effectively unify
university faculties, disciplines and several major projects,
professionally and economically. In consideration of the "core"
regarding the Center’s vision, it will continue to be a flagship
representative of superbly advanced technologies and will position
itself as a global equal, a common denominator, willing and able to
immediately network among other 3D Print Technology entities throughout
the world. In consideration of these changes, the leadership of the 3D
Printing and Technology Center genuinely envision an entity in which it
is capable in concentrating deeper into relevant areas aligned with a
successful future. Addtionally, a stretch goal is currently undergoing
discussion in which increased levels of professional support regarding
the PTE's R, D & I activities are accompanied with an increase in
expertise and response time.
“In retrospect, the essential idea in support of creating the PTE3D
project dates back to 2015,” remarked Dr. Péter Maróti. “Dr. József
Bódis, the former Rector of the University of Pécs, and currently the
State Secretary for Education, was aiming for a multidisciplinary
research center from the onset, strategically combing research teams
working at various faculties of the university using 3D technologies as
the common denominator. The Faculty of Medicine, the Faculty of
Economics, the Faculty of Engineering and Informatics, the Faculty of
Arts and the Faculty of Natural Sciences all were active and willing
participants in the effective development of the PTE3D concept. Soon
thereafter, the Rector commissioned Dr. Miklós Nyitrai, now the current
Dean of the PTE Faculty of Medicine, as the Director of the Research
Center.
“We successfully applied to the National Office for Research and
Innovation, which supported the concept including funding valued at more
than 1.8 billion forints. Last March, we hosted a Grand Opening of the
independently owned PTE3D project's 600 square meter headquarters
located in the Faculty of Technology and Information Technology,” adds
Dr. Maroti.
Today, the 3D Center employs a variety of 3D printing techniques. One
is the well-known, FFF (Fused Filament Fabrication), a process which
extracts layers of plastic from thermoplastic polymer fibers to make the
3D form. In consideration of these small, economically-priced printers,
the 3D Center now can manufacture inexpensive, fast, custom-made
plastic objects. The PTE3D Center also uses selective laser sintering
(SLS) as a dependable form of technology. Remarkably, both these two
printing techniques are frequently used in the research center, for
example, in the development of upper limb prostheses. In addition, there
are several industrial-scale machines based on photopolymer printing
techniques. “They illuminate liquid resin with light or laser, layer by
layer. The extremely fine resolution, up to 16 micrometers, can be
achieved using this method. This approach is ideally suitable in the
manufacturing of oral surgery design templates, or orthodontic devices,”
emphasizes Dr. Maróti.
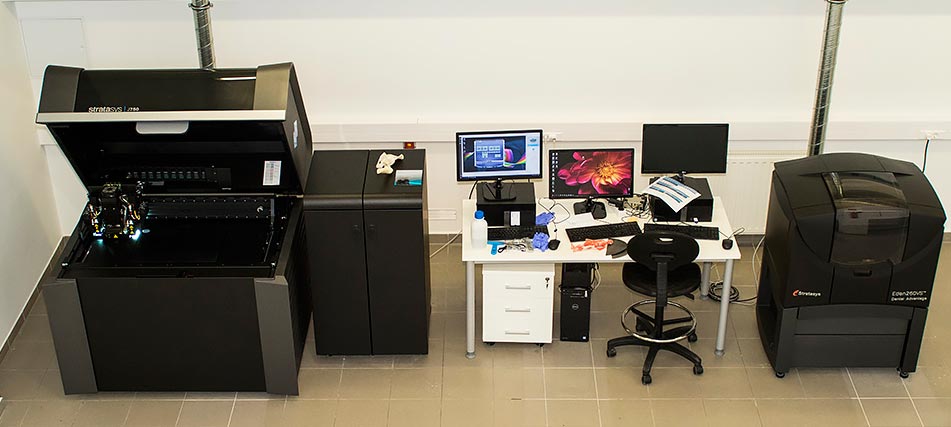
Additionally, Dr. Maroti describes, how in the last three years, a
plethora of ideas have been floated among staff, specifically, what
areas have yet not been probed in which 3D printing might offer immense
benefits. Several of the architects aligned to the Faculty of
Engineering and Information Technology are in healthy collaboration with
their colleagues of the Fine Arts Faculty regarding the construction of
uniquely designed homes facilitating in the use of concrete printing.
Recently, the PTE3D Center was besieged by an uptick in a wide range
of external orders, originating from all corners of the country, in
which the inquiries ranged from individuals to industrial complexes. Dr.
Maroti continues, “There was an individual who desired to print a
custom-designed vase, another individual was craving for a 3D printed
element in support of his vacuum cleaner, and one of our faculties
awarded the TDK winning students with owl figures manufactured using 3D
print technology. Additionally, there were also industrial
representatives who forwarded a request for specialized parts
desperately needed for massive plant production.”
Since the 3D Print and Vision Center is aligned as a genuine academic
research center, it is prohibited from accruing a profit. However, in
consideration of external orders, it is lawful to cover the operational
costs. Lastly, the staff admittedly benefits from the overall
experience.
“Distinctly, this is an important goal in support of the team and we
want to maintain our openness and flexibility, yet it is cumbersome to
focus on our mission and ensure a timely response regarding incoming
orders, all the while simultaneously designing and implementing various
tools in response to the various medical technological projects assigned
to the center.”
“Specifically, this is primarily the reason we inevitably determined
it was in the best interests of all participating faculties to
restructure the fundamental activities and re-position the center’s
directive,” states Dr. Maroti.
“This is an excellent opportunity regarding growth, and affords staff
to streamline production and maintain a high level of quality
assurance, all of which was formerly emphasized at the Biomedical
Engineering Center. The 3D Center is expected to remain an important
part of the new organization, yet, of course, based on agreements with
other collaborative research teams and research projects, we can
delineate our competencies and operational goals far more precisely than
before. We intend to primarily focus on our own medical technological
developments, and if once the center has the additional capacity in
support of addtional orders, naturally, we will be happy to oblige,”
summarizes Dr. Péter Maróti.
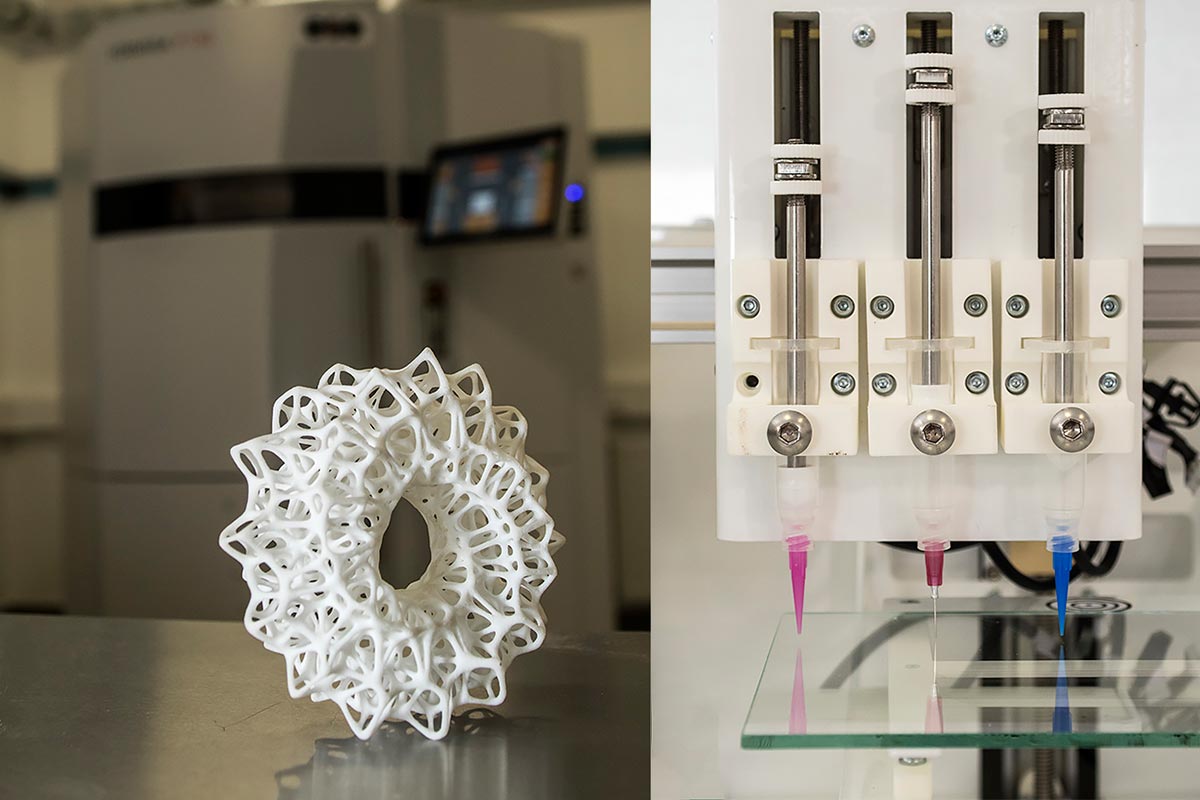
Within the new umbrella organization, based on past experiences, six
new workgroups are being created and 3D printing is an integral link to
all the teams. To cite an example, the Medical Material Technology
Research Group examines the materials used in 3D printing, including the
characteristics and behavior of polymers and composites. They also
experiment with custom-developed materials. Specifically, how does one
alter the structure and characteristics of thermoplastic plastics by
adding calcium carbonate or carbon concentrates?
However, the study regarding different silicones is also part of the
Medical Material Technology Research Group’s basic research, and their
application is already closely linked to another workgroup, namely the
Health Simulations Workgroup. This area already has an astonishingly
lengthy, reputable history within the University of Pécs, of which, the
MediSkillsLab Simulation Education Center has been successfully
operating since 2015 within the Faculty of Medicine. It is here, for
example, in which 3D printing is used to replace the worn-out
functionality regarding the numerous ALS (Advanced Life Support) medical
mannequins, which are considered cutting-edge technology throughout
Europe and obviously immensely beneficial in graduate and postgraduate
training. Today, medical students practice laryngeal pruning on an
intensely realistic, artificial laryngeal or practice medical procedures
and operations on the center’s very own self-developed bleeding
artificial skin or on a realistic artificial arm.
Strikingly, they are also using artificial brain chambers, bones, and
tools in support of practicing wound healing. 3D printing is also used
for routine maintenance regarding the affectionately referred to, “high
loyalty simulators.” These are human body imitation models loaded with a
robust, serious software background. They perfectly simulate various
life functions and including subtle, human-like disturbances, and even
respond to medical interventions. Many injections of venous injections
and cardiac arrhythmias can be practiced using these fascinating human
simulators.
Today, dedicated workgroups are heavily involved in the development
of healthcare software solutions and bio-printing. The latter is perhaps
one of the most innovative areas regarding medical-technology, which
serves in driving the imagination of science fiction fans. For example,
various organoids are created, i.e., living tissue samples from living
cells, artificially. In regards to these artifically developed living
tissues, researchers study the underlying causes of diseases and the
mechanism of action associated with various pharmaceuticals at the
molecular level. In the Bioprinting Research Center at Pécs, for
example, staff print lung tissue and examine the molecular background
aligned with lung cancer, inflammatory and fibrotic diseases and carries
out related drug experiments.
The Neurorehabilitation workgroup implements 3D printing primarily to
make various prostheses. Dr. Maróti Péter emphasizes how staff
primarily focuses upon the creation of self-developed upper limb
prostheses. These developments are unique on the Hungarian market and it
is a testament of the Neurorehabilitation’s ingenuity.
“Engineers, IT professionals and medical doctors are now
comprehensively working together in this area. After fitting the upper
limb prosthesis to the patient, the electrical signals regarding the
muscle function are detected by electrodes, thus, they can execute the
motion command. A 3D printed prosthesis can be far more accurately
customized to the individual needs of the client, and can be
manufactured much faster and more cost-effectively than when compared to
conventionally manufactured artificial limbs. We are still in the
production phase of the prototype, however, we are currently
strategizing product development with a serious investor group.
Theoretically, we need one and a half or two years to make this as an
actual medical product available to clients,” Dr. Maroti stated.
Lastly, a dedicated working group will combine their professional
efforts towards medical robotics, remote diagnostics and remote surgical
intervention. The astonishing development of medical robotics
effectively demonstrates, it is now entirely possible to carry out
operations from afar using remote control and internet technology.
The emerging "super-research center" will attempt to maximize the
potential linking regarding the different ways in approach and thinking
throughout a wide variety of disciplines, thereby creating real
synergies. In consideration of the interdisciplinary approach witnessed
in the last century, and as a result, now offers a new impetus to the
previously stagnating disciplines, it is possible to imagine what new
approaches and innovative solutions can by accessed by linking research
and innovation topics which are now soaring.
Dr. Peter Maroti emphasizes how 3D printing alone is one of the
fastest growing innovative areas in the world including new printing
materials, processes and applications rapidly emerging on nearly a daily
basis. Connecting this development curve to other, equally innovative
or "high-tech" projects, promises improvement, efficiency and speed
regarding these projects.
“Today, there are several world-class success stories regarding
several topics, such as the use of new medical simulation techniques or
the manufacturing of prostheses, which can bring Hungary to the
forefront of 3D printing,” forecasts Dr. Maroti.